PVD technology appeared in the late 1970s. The films prepared have the advantages of high hardness, low friction coefficient, good wear resistance and chemical stability. The initial successful application in the field of high-speed steel cutting tools attracted great attention from manufacturing industries around the world. While developing high-performance and high-reliability coating equipment, people also conducted more in-depth coatings on cemented carbide and ceramic cutting tools. layer application research. Compared with the CVD process, the PVD process has a low processing temperature and has no effect on the bending strength of the tool material below 600°C; the internal stress state of the film is compressive stress, which is more suitable for coating precision and complex carbide tools; PVD The process has no adverse impact on the environment and is in line with the development direction of modern green manufacturing. At present, PVD coating technology has been widely used in the coating treatment of carbide end mills, drill bits, step drills, oil hole drills, reamers, taps, indexable milling inserts, special-shaped tools, welding tools, etc.
What does PVD coating mean?
Meaning: PVD (Physical Vapor Deposition) physical vapor deposition technology: means that under vacuum conditions, physical methods are used to vaporize the material source - solid or liquid surface into gas atoms, molecules or partially ionized into ions, and pass through low-pressure gas (or plasma body) process, a technology that deposits thin films with special functions on the surface of a substrate.
The PVD coating we usually know is the so-called vacuum coating technology. Vacuum coating technology and processes have been widely used in vacuum coating processing companies. PVD coating is mainly coated under vacuum conditions. Its usage industries and market prospects are also It is very broad, and the process flow and construction conditions of PVD coating are not relatively complicated. The corresponding PVD coating is vacuum ion plating under vacuum conditions through a PVD coating machine.
PVD coating can be completed in one go, and the PVD coating production process is stable, saving energy and time. The process flow of PVD coating must first process the product in advance, remove oil stains and dust from the surface of the processed product, wait for the product to dry, spray primer and then level it, followed by the main PVD coating process, and then wait for curing before packaging. Packing. The construction conditions of PVD coating must remove dust and clean the product. If the dust removal effect is not good, the PVD coating effect will be poor, which is called film peeling of the coated product. Similarly, if the cleaning products are not in place, the same film peeling will also occur. Phenomenon.
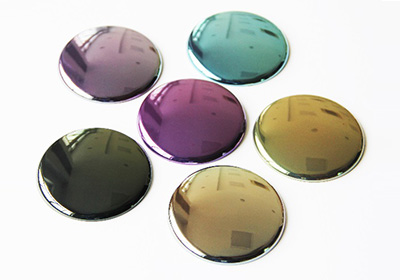